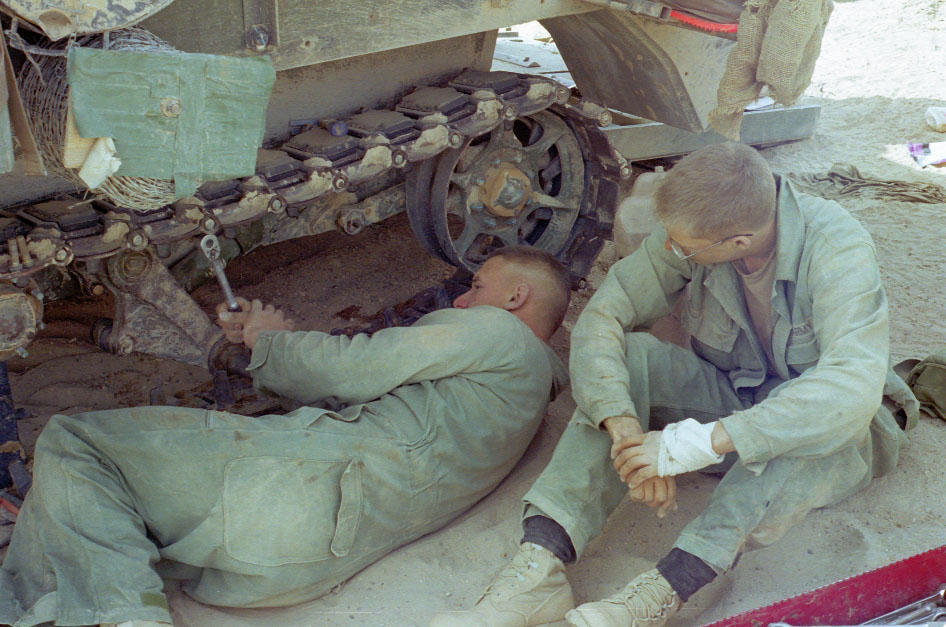
A Team Above all Others: Story 2
I arrived in Bamberg Germany in July of 2001 assigned to 54th Engineer Battalion, destined to lead a maintenance team. I was the senior most SGT with a little over 11 years behind me. Six of those as a SGT. Now I don’t mention this like it’s a badge of honor, but I came with a good amount of experience behind me.
When I arrived and because I out ranked every other Sergeant, I should have led a maintenance team. 54th, was broken down into 4 teams: HQ, A, B, and C companies. The first three had Staff Sergeants or higher as their maintenance chiefs, so I wasn’t taking those. C company, had a Sergeant I out ranked, but they just gave him the job three weeks before. It was decided I would go to B company’s team and take over when the maintenance chief left in six months.
The Failed Maintenance Program
I was both disappointed and happy with the decision. It was my first time being assigned to a Mechanized Combat Engineer Battalion. I wasn’t as familiar with the equipment, and time would fix that. I was a construction equipment repairer. My previous assignment was in a construction battalion in Alaska. Before that was a waterborne transportation battalion. Unknowingly, that decision placed me on a trajectory for success.
I finally became a maintenance chief in mid-November 2002 for A company. Leadership removed the Staff Sergeant in charge from the position due to his failures. I had been Motor Sergeant before, and lead large maintenance sections, but I had never taken over a team that was in such chaos. I remember walking in the first day and asking what was wrong with the three or four vehicles in the bays. Not one mechanic could tell me what was wrong.
Equipment breaks down, that is inevitable. For the military though, nonoperational equipment is bad for potential war. We must report our operational rate daily. The expectation is to maintain a 90% or better operational rate. Anything below the and you must explain why. Maybe you’re waiting on parts, which is acceptable. What leadership does not want to hear is, “we are still trying to figure out the problem,” especially after many days.
A company’s operational rate was around 50% when I walked into that maintenance shop. The mechanics were still trying to figure out what was wrong with equipment, days, even weeks later. Mechanics ordered a driveshaft for a dump truck incorrectly three times. Management, mentor-ship, and leadership at its worst, and I was tasked with turning this shop around.
The Maintenance Struggle
As I laid out my plan to turn the team around and quickly improve the operational rate, we took time off for Thanksgiving. Between Thanksgiving and Christmas, not much else occurred, it never does. Mechanics took leave and other delays occurred. Bad timing was part of my struggle. I wasn’t making any headway. On January 2nd, 2003, another blow to my ability to raise the operational rate occurred. A company tasked as the pusher unit for the Deployment Processing Center (DPC) at Ramstein Air Force Base, Germany. The mission grew from needing just a plused-up platoon to 90% of the company. Left behind were a few mechanics with me and an expectation to improve the operation rate. I just could not get ahead.
Due to the rising conflict in Iraq, C company got called up to deploy. Told to give them anything and everything they needed, we did just that. They took any repair parts we might have had stored away that they needed. The even took a pack (engine and transmission combination) out of our Commander’s M113 Personnel Carrier to put in one of theirs. The thought was: we had time to get a new pack for our vehicle since we were not deploying.
Shockingly, two weeks after we loaded C company’s equipment on a train bound for the port, the they told the rest of 54th Engineer Battalion to deploy. We had two weeks to get everything ready and loaded on to trains. There was just two problems. First the company was still at Ramstein as the pusher unit. Second, I was unable to get much of the equipment repaired by then. We dragged a lot of equipment onto the trains; repairs would have to take place in Kuwait.
Our deployment to Kuwait and our enviable invasion of Iraq, would start with a struggle due to a failed maintenance program. Like a phoenix rising again, my team would step up. They repaired every piece of broken equipment before we rolled across the border in to Iraq.
Read my story, “The miracle workers,” part of the A Team Above all Others series, to get a glimpse of how we overcame our struggles.
Did you like this story? Leave your comments below. Do you have a story you want to contribute? Use the “I Have a Story” button to contact us. We will help you tell your story.